Jeudi matin, découverte du site de Miribel du groupe ABB France
ABB est un leader des technologies de pointe au service de ses clients au sein de 4 domaines : les utilités, l’industrie, le transport et les infrastructures. Ce groupe vise la digitalisation des industries afin d’augmenter la valeur clients. De plus, il développe des technologies de pointe dans le cadre de l’amélioration des moyens de transports.
Les activités d’ABB sont organisées en quatre divisions elles-mêmes subdivisées en Business Unit afin de couvrir chaque catégorie de produits et d’industries.
Au sein de trois ateliers, nous avons pu découvrir des outils développés par ABB pour ses clients. Tout d’abord ABB a développé une interface digitale permettant à ses clients de faire remonter toutes les informations énergétiques de leur infrastructure (entrepôt, industrie, bureaux, magasins…), les anomalies pour optimiser les interventions de maintenance.
Une nouvelle plateforme numérique unifiée et transversale combine cloud computing, passerelle de supervision et de commande, appareils, systèmes, solutions et services pour aider les clients à en savoir plus, à agir plus et à agir mieux.
Louise BIGOT
L'après-midi était réservé au Stage dating.
Les étudiants ont pu échanger et profiter des différentes opportunités de stages que les entreprises ont proposés.
Etaient présents le Groupe GERARD PERRIER INDUSTRIE , le Groupe EFINOR, le Groupe PIROUX Industrie, BREVET CARROSSERIE, le POLE FORMATION DES INDUSTRIES DE L’AIN – AFPMA, CONDUCTIX, GEIQ INDUSTRIE DE L’AIN, groupe ATLANTIC ainsi que la Chaire industrie 4.0 de l'UIMM de l'Ain et de Grenoble INP Génie industriel.
Piroux v
endredi matin
Notre vendredi matin a démarré par la présentation de l’entreprise Piroux située à Saint Étienne du Bois et Treffort (15 min de Bourg en Bresse). Les industriels nous ont présenté leur entreprise, le réseau et leurs produits. L'entreprise Piroux possède 5 sites en France et 3 en Roumanie. Une fois équipés de nos équipements de protection individuels nous avons commencé la visite du premier site par le traitement Cataphorèse qui permet l’application d’un revêtement protecteur des pièces métalliques. Certaines pièces sont liv
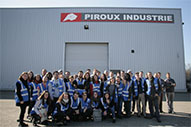
rées directement aux clients après cette étape alors que d’autres nécessitent une étape de peinture. Nous avons aussi pu observer les étapes de masticage assemblage et de soudure. Sur le second site, ce sont les étapes de peinture, presse et pliage qui nous ont été expliquées. Le lien avec la Roumanie a aussi permis des échanges humains dont un ingénieur Roumain venu en France pour apporter son analyse et programmer un robot. Merci de nous avoir ouvert les portes de l'entreprise Piroux.
Chez Piroux, ils se plient en Ain pour vous !
Cyrielle Barrilliet et ses copains
Dans l’après-midi du vendredi, la moitié des étudiants a été reçue au sein de l’entreprise Jacquemet.
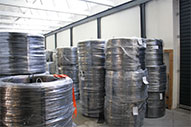
Cette entreprise possède 5 sites, 4 en France et le dernier en Roumanie. Trois d’entre eux sont spécialisés dans la production de ressorts, de petit diamètre, de gros diamètre et de ressorts plats, et les deux autres, dont celui situé à St Martin du Fresne, que nous avons visité, ont pour cœur de métier le travail du fil métallique.
Tout d’abord spécialisé dans la confection d’aiguilles à tricoter, cet atelier a ensuite bifurqué dans les années 1980 vers la production de rayons de vélo en aluminium, puis de changer une nouvelle fois de produit phare plus récemment, en fournissant notamment de nombreux produits à l’entreprise Décathlon, leur principal client actuel, tels que des panières de rangement en grille métallique ou encore en fabriquant
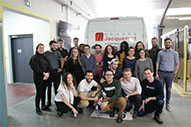
des produits destinés au marché de l’équipement automobile, comme des structures internes de pare-soleil.
Nous avons pu visiter l’intégralité des locaux, découvrant les machines permettant le dressage, le cintrage, la soudure et le marquage des fils métalliques afin de réaliser les différents produits. Une partie de ces équipements est automatisée tandis que certaines opérations restent manuelles. Des machines de tailles différentes permettent de s’adapter à des fils de diamètre et de matériau variés. Le stockage sur site est très réduit, composé majoritairement des matières premières et des encours, ainsi que de quelques produits finis, conditionnés et prêts à l’envoi. L’atelier comprend également un espace de prototypage qui permet de fabriquer un petit nombre de produits destinés à la validation des projets avec le client. Enfin, l’entreprise produit elle-même son outillage dans un atelier mécanique, où sont réalisés sur un centre d’usinage les outils nécessaires à la soudure ou aux presses.
Chloé Demaret
L'autre moitié était chez Chalon Megard
La visite a commencé par une présentation de l’entreprise. Elle fabrique des lignes entières de production de fromage depuis 100 ans, mais peut aussi implanter des usines (en Bretagne par exemple). A l’origine, il s’agissait d’une entreprise de chaudronnerie. Chalon Megard apporte des solutions complètes aux fromageries et s’adapte aux besoins de ses clients. De plus, ils testent leur équipement dans l’atelier avant de les livrer aux clients.
La suite de la visite fut la découverte de l’atelier. Nous avons pu y découvrir les principaux éléments de la ligne de production de fromage. C’est un atelier très complet car ils fabriquent tous les éléments de la ligne de production ainsi que les composants.
Pour ce qui est de l’accueil, celui-ci fut chaleureux et agréable. De plus, cette entreprise est en demande de stagiaires et a de nombreux postes à pourvoir.
Le mot du dirigeant : « Le monde change, il faut changer avec. »
Amélie Auffret-Carriou
Un grand merci à Marie-Hélène Lebranchu, Emmanuelle Perret, Catherine Vial de l'UIMM de l'Ain pour l'organisation mais aussi à Charlotte Nicollay et Laudyce Brocherioux pour l'organisation logistique.